What is the Mainstream Chip Resistor Production Process?
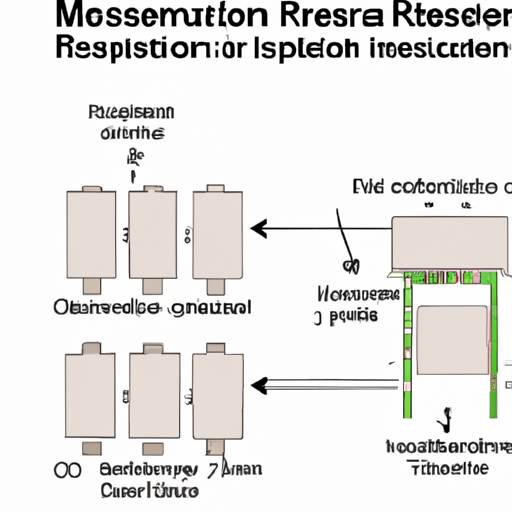
I. Introduction
Chip resistors, also known as surface mount resistors, are essential components in modern electronic devices. These tiny components play a critical role in controlling the flow of electric current, ensuring that circuits function correctly and efficiently. As the demand for smaller, more efficient electronic devices continues to rise, the production of chip resistors has evolved into a sophisticated process that combines advanced materials science with cutting-edge manufacturing techniques. This blog post will explore the mainstream chip resistor production process, detailing each step from raw materials to final testing and quality control.
II. Raw Materials
A. Types of Materials Used
The production of chip resistors begins with the selection of high-quality raw materials. The primary materials used in chip resistors can be categorized into two main types:
1. **Conductive Materials**: These materials are responsible for the resistive properties of the chip. Common conductive materials include metal films, such as nickel-chromium, and carbon-based compounds. Metal film resistors are known for their precision and stability, while carbon resistors are often used for their cost-effectiveness.
2. **Substrate Materials**: The substrate serves as the base for the resistor and is typically made from ceramic or glass. Ceramic substrates are favored for their excellent thermal stability and electrical insulation properties, making them ideal for high-performance applications.
B. Quality Control of Raw Materials
Quality control is paramount in the production of chip resistors. Manufacturers must ensure that the raw materials meet stringent specifications to guarantee the performance and reliability of the final product. This involves rigorous testing and inspection of materials before they enter the production line.
C. Sourcing and Sustainability Considerations
In recent years, there has been a growing emphasis on sustainability in the electronics industry. Manufacturers are increasingly sourcing materials from suppliers that adhere to environmentally friendly practices. This includes using recycled materials and ensuring that the extraction of raw materials does not harm the environment.
III. Design and Specifications
A. Determining Resistance Values and Tolerances
Before production can begin, engineers must determine the specific resistance values and tolerances required for the chip resistors. This involves understanding the application in which the resistors will be used, as different applications may require different specifications.
B. Design Considerations for Different Applications
The design of chip resistors must take into account various factors, including size, power rating, and temperature coefficient. For instance, resistors used in high-frequency applications may require different design parameters compared to those used in power electronics.
C. Role of CAD Software in Design
Computer-Aided Design (CAD) software plays a crucial role in the design process. Engineers use CAD tools to create detailed models of the resistors, allowing for precise adjustments and optimizations before moving to the manufacturing stage.
IV. Manufacturing Process
The manufacturing process of chip resistors involves several key steps, each of which is critical to ensuring the quality and performance of the final product.
A. Step 1: Substrate Preparation
The first step in the manufacturing process is substrate preparation. This involves cleaning and surface treatment to remove any contaminants that could affect adhesion and performance. The substrates are then cut to the desired size, ensuring uniformity across batches.
B. Step 2: Deposition of Resistive Material
Once the substrates are prepared, the next step is the deposition of the resistive material. Various techniques can be employed for this process, including:
1. **Sputtering**: A physical vapor deposition technique that involves ejecting material from a target onto the substrate, creating a thin film of resistive material.
2. **Screen Printing**: A more traditional method where a paste containing the resistive material is pushed through a mesh screen onto the substrate.
Thickness control and uniformity are critical during this step, as variations can lead to inconsistent resistance values.
C. Step 3: Patterning
After the resistive material is deposited, the next step is patterning. This is typically achieved through a photolithography process, where a light-sensitive material is applied to the substrate. The desired pattern is then exposed to light, and the unexposed areas are removed, leaving behind the resistive pattern.
Etching techniques may also be employed to further refine the pattern and remove excess material, ensuring that the resistive elements are precisely defined.
D. Step 4: Termination
The termination process involves applying metal terminations to the ends of the resistive element. These terminations are crucial for ensuring good electrical contact with the circuit board. Manufacturers must consider solderability and adhesion during this step to ensure reliable connections.
E. Step 5: Sintering and Curing
The final step in the manufacturing process is sintering and curing. This involves heating the resistors to a specific temperature to enhance the bonding of materials and improve electrical properties. Temperature control is vital during this stage, as it can significantly affect the performance and reliability of the resistors.
V. Testing and Quality Control
Once the chip resistors are manufactured, they undergo rigorous testing and quality control to ensure they meet the required specifications.
A. Electrical Testing Methods
Electrical testing methods are employed to measure the resistance values and verify tolerances. This may involve using precision measurement equipment to ensure that each resistor meets the specified criteria.
B. Mechanical Testing
Mechanical testing is also essential to assess the durability and reliability of the resistors. This includes thermal cycling tests, which evaluate how the resistors perform under varying temperature conditions, as well as vibration and shock tests to simulate real-world conditions.
C. Final Inspection and Packaging
After testing, the resistors undergo a final inspection to ensure they meet quality standards. Once approved, they are packaged for shipment, ensuring that they are protected from damage during transportation.
VI. Environmental and Regulatory Considerations
A. Compliance with Industry Standards
Manufacturers must comply with various industry standards, such as RoHS (Restriction of Hazardous Substances) and REACH (Registration, Evaluation, Authorisation, and Restriction of Chemicals). These regulations ensure that chip resistors are produced in an environmentally responsible manner and do not contain harmful substances.
B. Environmental Impact of Production
The production of chip resistors can have environmental impacts, including waste generation and energy consumption. Manufacturers are increasingly adopting sustainable practices to minimize their ecological footprint, such as reducing waste and improving energy efficiency.
C. Recycling and Disposal of Chip Resistors
As the electronics industry continues to grow, the need for responsible recycling and disposal of electronic components, including chip resistors, becomes more critical. Manufacturers are exploring ways to recycle materials and reduce the environmental impact of discarded components.
VII. Future Trends in Chip Resistor Production
A. Advances in Materials Science
The field of materials science is continually evolving, leading to the development of new materials that can enhance the performance of chip resistors. Innovations in nanotechnology and composite materials may lead to resistors with improved stability, accuracy, and thermal performance.
B. Automation and Industry 4.0
The integration of automation and Industry 4.0 technologies is transforming the manufacturing landscape. Smart factories equipped with advanced robotics and data analytics can improve efficiency, reduce production costs, and enhance quality control in chip resistor production.
C. Customization and Miniaturization Trends
As electronic devices become smaller and more complex, the demand for customized and miniaturized chip resistors is on the rise. Manufacturers are exploring ways to produce resistors that meet specific customer requirements while maintaining high performance and reliability.
VIII. Conclusion
In conclusion, the production process of chip resistors is a complex and highly specialized endeavor that involves multiple stages, from raw material selection to final testing and quality control. As the demand for electronic devices continues to grow, the importance of high-quality chip resistors cannot be overstated. Manufacturers must prioritize innovation and sustainability to meet the evolving needs of the industry. With advances in materials science, automation, and customization, the future of chip resistor production looks promising, paving the way for even more efficient and reliable electronic devices.
What is the Mainstream Chip Resistor Production Process?
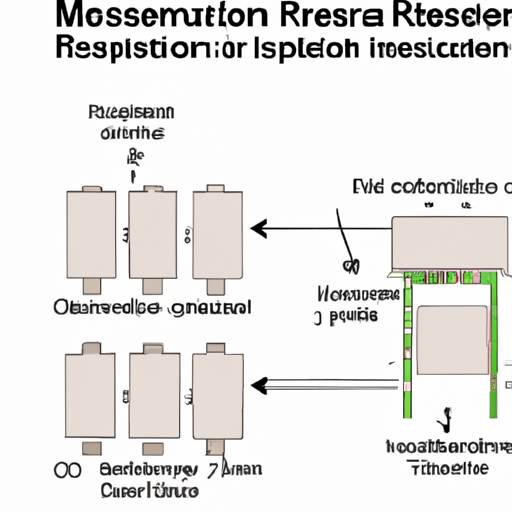
I. Introduction
Chip resistors, also known as surface mount resistors, are essential components in modern electronic devices. These tiny components play a critical role in controlling the flow of electric current, ensuring that circuits function correctly and efficiently. As the demand for smaller, more efficient electronic devices continues to rise, the production of chip resistors has evolved into a sophisticated process that combines advanced materials science with cutting-edge manufacturing techniques. This blog post will explore the mainstream chip resistor production process, detailing each step from raw materials to final testing and quality control.
II. Raw Materials
A. Types of Materials Used
The production of chip resistors begins with the selection of high-quality raw materials. The primary materials used in chip resistors can be categorized into two main types:
1. **Conductive Materials**: These materials are responsible for the resistive properties of the chip. Common conductive materials include metal films, such as nickel-chromium, and carbon-based compounds. Metal film resistors are known for their precision and stability, while carbon resistors are often used for their cost-effectiveness.
2. **Substrate Materials**: The substrate serves as the base for the resistor and is typically made from ceramic or glass. Ceramic substrates are favored for their excellent thermal stability and electrical insulation properties, making them ideal for high-performance applications.
B. Quality Control of Raw Materials
Quality control is paramount in the production of chip resistors. Manufacturers must ensure that the raw materials meet stringent specifications to guarantee the performance and reliability of the final product. This involves rigorous testing and inspection of materials before they enter the production line.
C. Sourcing and Sustainability Considerations
In recent years, there has been a growing emphasis on sustainability in the electronics industry. Manufacturers are increasingly sourcing materials from suppliers that adhere to environmentally friendly practices. This includes using recycled materials and ensuring that the extraction of raw materials does not harm the environment.
III. Design and Specifications
A. Determining Resistance Values and Tolerances
Before production can begin, engineers must determine the specific resistance values and tolerances required for the chip resistors. This involves understanding the application in which the resistors will be used, as different applications may require different specifications.
B. Design Considerations for Different Applications
The design of chip resistors must take into account various factors, including size, power rating, and temperature coefficient. For instance, resistors used in high-frequency applications may require different design parameters compared to those used in power electronics.
C. Role of CAD Software in Design
Computer-Aided Design (CAD) software plays a crucial role in the design process. Engineers use CAD tools to create detailed models of the resistors, allowing for precise adjustments and optimizations before moving to the manufacturing stage.
IV. Manufacturing Process
The manufacturing process of chip resistors involves several key steps, each of which is critical to ensuring the quality and performance of the final product.
A. Step 1: Substrate Preparation
The first step in the manufacturing process is substrate preparation. This involves cleaning and surface treatment to remove any contaminants that could affect adhesion and performance. The substrates are then cut to the desired size, ensuring uniformity across batches.
B. Step 2: Deposition of Resistive Material
Once the substrates are prepared, the next step is the deposition of the resistive material. Various techniques can be employed for this process, including:
1. **Sputtering**: A physical vapor deposition technique that involves ejecting material from a target onto the substrate, creating a thin film of resistive material.
2. **Screen Printing**: A more traditional method where a paste containing the resistive material is pushed through a mesh screen onto the substrate.
Thickness control and uniformity are critical during this step, as variations can lead to inconsistent resistance values.
C. Step 3: Patterning
After the resistive material is deposited, the next step is patterning. This is typically achieved through a photolithography process, where a light-sensitive material is applied to the substrate. The desired pattern is then exposed to light, and the unexposed areas are removed, leaving behind the resistive pattern.
Etching techniques may also be employed to further refine the pattern and remove excess material, ensuring that the resistive elements are precisely defined.
D. Step 4: Termination
The termination process involves applying metal terminations to the ends of the resistive element. These terminations are crucial for ensuring good electrical contact with the circuit board. Manufacturers must consider solderability and adhesion during this step to ensure reliable connections.
E. Step 5: Sintering and Curing
The final step in the manufacturing process is sintering and curing. This involves heating the resistors to a specific temperature to enhance the bonding of materials and improve electrical properties. Temperature control is vital during this stage, as it can significantly affect the performance and reliability of the resistors.
V. Testing and Quality Control
Once the chip resistors are manufactured, they undergo rigorous testing and quality control to ensure they meet the required specifications.
A. Electrical Testing Methods
Electrical testing methods are employed to measure the resistance values and verify tolerances. This may involve using precision measurement equipment to ensure that each resistor meets the specified criteria.
B. Mechanical Testing
Mechanical testing is also essential to assess the durability and reliability of the resistors. This includes thermal cycling tests, which evaluate how the resistors perform under varying temperature conditions, as well as vibration and shock tests to simulate real-world conditions.
C. Final Inspection and Packaging
After testing, the resistors undergo a final inspection to ensure they meet quality standards. Once approved, they are packaged for shipment, ensuring that they are protected from damage during transportation.
VI. Environmental and Regulatory Considerations
A. Compliance with Industry Standards
Manufacturers must comply with various industry standards, such as RoHS (Restriction of Hazardous Substances) and REACH (Registration, Evaluation, Authorisation, and Restriction of Chemicals). These regulations ensure that chip resistors are produced in an environmentally responsible manner and do not contain harmful substances.
B. Environmental Impact of Production
The production of chip resistors can have environmental impacts, including waste generation and energy consumption. Manufacturers are increasingly adopting sustainable practices to minimize their ecological footprint, such as reducing waste and improving energy efficiency.
C. Recycling and Disposal of Chip Resistors
As the electronics industry continues to grow, the need for responsible recycling and disposal of electronic components, including chip resistors, becomes more critical. Manufacturers are exploring ways to recycle materials and reduce the environmental impact of discarded components.
VII. Future Trends in Chip Resistor Production
A. Advances in Materials Science
The field of materials science is continually evolving, leading to the development of new materials that can enhance the performance of chip resistors. Innovations in nanotechnology and composite materials may lead to resistors with improved stability, accuracy, and thermal performance.
B. Automation and Industry 4.0
The integration of automation and Industry 4.0 technologies is transforming the manufacturing landscape. Smart factories equipped with advanced robotics and data analytics can improve efficiency, reduce production costs, and enhance quality control in chip resistor production.
C. Customization and Miniaturization Trends
As electronic devices become smaller and more complex, the demand for customized and miniaturized chip resistors is on the rise. Manufacturers are exploring ways to produce resistors that meet specific customer requirements while maintaining high performance and reliability.
VIII. Conclusion
In conclusion, the production process of chip resistors is a complex and highly specialized endeavor that involves multiple stages, from raw material selection to final testing and quality control. As the demand for electronic devices continues to grow, the importance of high-quality chip resistors cannot be overstated. Manufacturers must prioritize innovation and sustainability to meet the evolving needs of the industry. With advances in materials science, automation, and customization, the future of chip resistor production looks promising, paving the way for even more efficient and reliable electronic devices.