What are the Product Standards for Fixed Resistors?
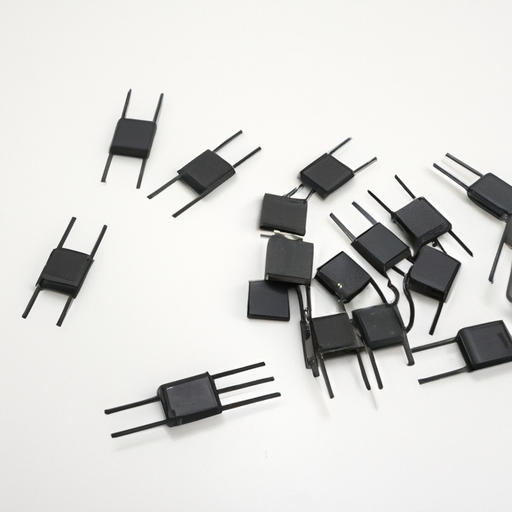
I. Introduction
In the world of electronics, fixed resistors play a crucial role in controlling current flow and voltage levels within circuits. These components are essential for the proper functioning of various electronic devices, from simple household appliances to complex industrial machinery. However, the reliability and performance of fixed resistors depend significantly on adherence to established product standards. This article aims to explore the product standards for fixed resistors, highlighting their importance, key standards, testing methods, compliance processes, and future trends.
II. Understanding Fixed Resistors
A. Basic Principles of Resistance
Resistance is a fundamental property of materials that impedes the flow of electric current. It is measured in ohms (Ω) and is determined by the material's resistivity, length, and cross-sectional area. Fixed resistors are designed to provide a specific resistance value, which remains constant under varying conditions. This stability is essential for ensuring predictable circuit behavior.
B. Types of Fixed Resistors
Fixed resistors come in various types, each with unique characteristics and applications:
1. **Carbon Composition Resistors**: Made from a mixture of carbon and a binding material, these resistors are known for their high energy absorption and ability to withstand high temperatures. However, they have a higher tolerance and lower stability compared to other types.
2. **Metal Film Resistors**: These resistors are constructed by depositing a thin layer of metal onto a ceramic substrate. They offer better stability, lower noise, and tighter tolerances, making them suitable for precision applications.
3. **Wirewound Resistors**: Made by winding a metal wire around a core, wirewound resistors can handle high power levels and are often used in applications requiring high precision and stability.
4. **Thin and Thick Film Resistors**: Thin film resistors are created by depositing a very thin layer of resistive material, while thick film resistors use a thicker layer. Both types offer excellent performance and are widely used in modern electronics.
C. Applications of Fixed Resistors in Electronic Circuits
Fixed resistors are utilized in a myriad of applications, including voltage dividers, current limiting, biasing active components, and signal conditioning. Their ability to maintain a consistent resistance value makes them indispensable in ensuring the reliability and functionality of electronic circuits.
III. Importance of Product Standards
A. Ensuring Reliability and Safety
Product standards are essential for ensuring that fixed resistors perform reliably under specified conditions. Adherence to these standards minimizes the risk of component failure, which can lead to safety hazards, equipment damage, and costly downtime.
B. Facilitating Compatibility and Interoperability
Standards promote compatibility between different manufacturers' products, allowing for seamless integration in electronic systems. This interoperability is crucial for designers and engineers who rely on components from various sources to create functional devices.
C. Enhancing Performance and Efficiency
By adhering to established standards, manufacturers can optimize the performance and efficiency of their fixed resistors. This optimization leads to improved energy consumption, reduced heat generation, and enhanced overall circuit performance.
D. Regulatory Compliance and Market Access
Compliance with product standards is often a prerequisite for market access. Regulatory bodies require that electronic components meet specific standards to ensure safety and environmental protection. Manufacturers that adhere to these standards can more easily enter global markets.
IV. Key Product Standards for Fixed Resistors
A. International Electrotechnical Commission (IEC) Standards
1. **IEC 60115 Series**: This series outlines the general requirements for fixed resistors, including performance, testing methods, and reliability. It serves as a foundational standard for manufacturers worldwide.
2. **IEC 60068 Series (Environmental Testing)**: This series specifies environmental testing methods for electronic components, including fixed resistors. It ensures that resistors can withstand various environmental conditions, such as temperature, humidity, and mechanical stress.
B. American National Standards Institute (ANSI) Standards
The ANSI/IEEE standards provide guidelines for electrical components, including fixed resistors. These standards focus on performance, testing, and safety requirements, ensuring that products meet the necessary criteria for reliability and functionality.
C. Joint Electron Device Engineering Council (JEDEC) Standards
JEDEC standards are crucial for semiconductor and electronic component manufacturers. They provide guidelines for testing and characterizing fixed resistors, ensuring consistency and reliability across the industry.
D. Other Relevant Standards
In addition to the aforementioned standards, regulations such as RoHS (Restriction of Hazardous Substances) and REACH (Registration, Evaluation, Authorisation, and Restriction of Chemicals) are essential for ensuring that fixed resistors are manufactured in an environmentally responsible manner.
V. Testing and Quality Assurance
A. Common Testing Methods for Fixed Resistors
1. **Resistance Measurement**: This fundamental test measures the resistance value of the resistor to ensure it meets specified tolerances.
2. **Temperature Coefficient Testing**: This test evaluates how the resistance value changes with temperature, ensuring that the resistor performs reliably across varying thermal conditions.
3. **Load Life Testing**: This test assesses the resistor's performance under continuous load over an extended period, simulating real-world operating conditions.
B. Quality Assurance Processes
1. **Incoming Inspection**: This process involves inspecting raw materials and components upon arrival at the manufacturing facility to ensure they meet quality standards.
2. **In-Process Quality Control**: Throughout the manufacturing process, quality control measures are implemented to monitor production and identify any deviations from standards.
3. **Final Product Testing**: Before products are shipped, final testing is conducted to verify that they meet all specified standards and performance criteria.
VI. Compliance and Certification
A. Importance of Compliance with Standards
Compliance with product standards is vital for manufacturers to ensure the safety, reliability, and performance of their fixed resistors. It also helps build trust with customers and regulatory bodies.
B. Certification Bodies and Their Roles
Several certification bodies play a crucial role in verifying compliance with product standards:
1. **Underwriters Laboratories (UL)**: UL provides safety certification for electronic components, ensuring they meet rigorous safety standards.
2. **TÜV Rheinland**: This organization offers testing and certification services for a wide range of products, including fixed resistors, focusing on quality and safety.
3. **Intertek**: Intertek provides testing, inspection, and certification services, helping manufacturers demonstrate compliance with international standards.
C. The Certification Process for Fixed Resistors
The certification process typically involves submitting samples for testing, undergoing inspections, and providing documentation to demonstrate compliance with relevant standards. Once certified, manufacturers can display certification marks on their products, signaling compliance to customers and regulatory bodies.
VII. Challenges in Meeting Product Standards
A. Variability in Manufacturing Processes
Manufacturers may face challenges in maintaining consistent quality due to variability in raw materials, production techniques, and equipment. This variability can impact the ability to meet established standards.
B. Evolving Technology and Standards
As technology advances, product standards must evolve to address new materials, manufacturing processes, and applications. Keeping up with these changes can be challenging for manufacturers.
C. Global Market Considerations
Navigating the complexities of global markets and varying regulatory requirements can pose challenges for manufacturers seeking to comply with product standards across different regions.
VIII. Future Trends in Fixed Resistor Standards
A. Innovations in Materials and Technology
The development of new materials and manufacturing techniques is likely to influence fixed resistor standards. Innovations such as nanotechnology and advanced ceramics may lead to improved performance and reliability.
B. The Impact of Sustainability and Environmental Regulations
As environmental concerns grow, standards will increasingly focus on sustainability. Manufacturers will need to adapt to regulations that promote eco-friendly practices and materials.
C. The Role of Digitalization in Standardization
Digitalization is transforming the manufacturing landscape, enabling more efficient production processes and enhanced quality control. This trend may lead to the development of new standards that leverage digital technologies for improved compliance and performance.
IX. Conclusion
In conclusion, product standards for fixed resistors are essential for ensuring the reliability, safety, and performance of these critical components in electronic circuits. Adherence to established standards not only facilitates compatibility and regulatory compliance but also enhances overall product quality. As technology continues to evolve, manufacturers must remain vigilant in adapting to new standards and challenges. The future of fixed resistor standards will likely be shaped by innovations in materials, sustainability considerations, and the ongoing digital transformation of the manufacturing industry. By prioritizing compliance with these standards, manufacturers can ensure that their products meet the demands of an ever-changing market while providing consumers with reliable and efficient electronic solutions.
What are the Product Standards for Fixed Resistors?
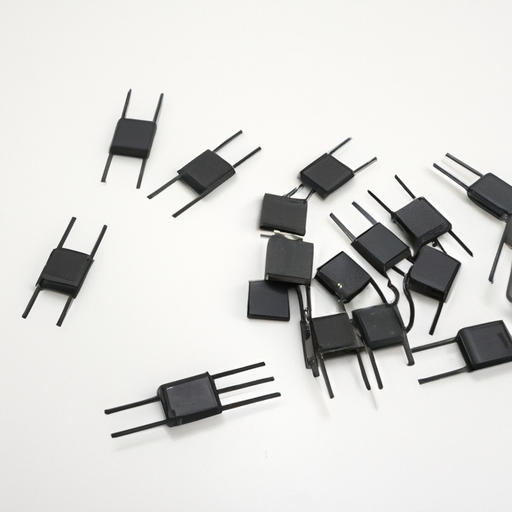
I. Introduction
In the world of electronics, fixed resistors play a crucial role in controlling current flow and voltage levels within circuits. These components are essential for the proper functioning of various electronic devices, from simple household appliances to complex industrial machinery. However, the reliability and performance of fixed resistors depend significantly on adherence to established product standards. This article aims to explore the product standards for fixed resistors, highlighting their importance, key standards, testing methods, compliance processes, and future trends.
II. Understanding Fixed Resistors
A. Basic Principles of Resistance
Resistance is a fundamental property of materials that impedes the flow of electric current. It is measured in ohms (Ω) and is determined by the material's resistivity, length, and cross-sectional area. Fixed resistors are designed to provide a specific resistance value, which remains constant under varying conditions. This stability is essential for ensuring predictable circuit behavior.
B. Types of Fixed Resistors
Fixed resistors come in various types, each with unique characteristics and applications:
1. **Carbon Composition Resistors**: Made from a mixture of carbon and a binding material, these resistors are known for their high energy absorption and ability to withstand high temperatures. However, they have a higher tolerance and lower stability compared to other types.
2. **Metal Film Resistors**: These resistors are constructed by depositing a thin layer of metal onto a ceramic substrate. They offer better stability, lower noise, and tighter tolerances, making them suitable for precision applications.
3. **Wirewound Resistors**: Made by winding a metal wire around a core, wirewound resistors can handle high power levels and are often used in applications requiring high precision and stability.
4. **Thin and Thick Film Resistors**: Thin film resistors are created by depositing a very thin layer of resistive material, while thick film resistors use a thicker layer. Both types offer excellent performance and are widely used in modern electronics.
C. Applications of Fixed Resistors in Electronic Circuits
Fixed resistors are utilized in a myriad of applications, including voltage dividers, current limiting, biasing active components, and signal conditioning. Their ability to maintain a consistent resistance value makes them indispensable in ensuring the reliability and functionality of electronic circuits.
III. Importance of Product Standards
A. Ensuring Reliability and Safety
Product standards are essential for ensuring that fixed resistors perform reliably under specified conditions. Adherence to these standards minimizes the risk of component failure, which can lead to safety hazards, equipment damage, and costly downtime.
B. Facilitating Compatibility and Interoperability
Standards promote compatibility between different manufacturers' products, allowing for seamless integration in electronic systems. This interoperability is crucial for designers and engineers who rely on components from various sources to create functional devices.
C. Enhancing Performance and Efficiency
By adhering to established standards, manufacturers can optimize the performance and efficiency of their fixed resistors. This optimization leads to improved energy consumption, reduced heat generation, and enhanced overall circuit performance.
D. Regulatory Compliance and Market Access
Compliance with product standards is often a prerequisite for market access. Regulatory bodies require that electronic components meet specific standards to ensure safety and environmental protection. Manufacturers that adhere to these standards can more easily enter global markets.
IV. Key Product Standards for Fixed Resistors
A. International Electrotechnical Commission (IEC) Standards
1. **IEC 60115 Series**: This series outlines the general requirements for fixed resistors, including performance, testing methods, and reliability. It serves as a foundational standard for manufacturers worldwide.
2. **IEC 60068 Series (Environmental Testing)**: This series specifies environmental testing methods for electronic components, including fixed resistors. It ensures that resistors can withstand various environmental conditions, such as temperature, humidity, and mechanical stress.
B. American National Standards Institute (ANSI) Standards
The ANSI/IEEE standards provide guidelines for electrical components, including fixed resistors. These standards focus on performance, testing, and safety requirements, ensuring that products meet the necessary criteria for reliability and functionality.
C. Joint Electron Device Engineering Council (JEDEC) Standards
JEDEC standards are crucial for semiconductor and electronic component manufacturers. They provide guidelines for testing and characterizing fixed resistors, ensuring consistency and reliability across the industry.
D. Other Relevant Standards
In addition to the aforementioned standards, regulations such as RoHS (Restriction of Hazardous Substances) and REACH (Registration, Evaluation, Authorisation, and Restriction of Chemicals) are essential for ensuring that fixed resistors are manufactured in an environmentally responsible manner.
V. Testing and Quality Assurance
A. Common Testing Methods for Fixed Resistors
1. **Resistance Measurement**: This fundamental test measures the resistance value of the resistor to ensure it meets specified tolerances.
2. **Temperature Coefficient Testing**: This test evaluates how the resistance value changes with temperature, ensuring that the resistor performs reliably across varying thermal conditions.
3. **Load Life Testing**: This test assesses the resistor's performance under continuous load over an extended period, simulating real-world operating conditions.
B. Quality Assurance Processes
1. **Incoming Inspection**: This process involves inspecting raw materials and components upon arrival at the manufacturing facility to ensure they meet quality standards.
2. **In-Process Quality Control**: Throughout the manufacturing process, quality control measures are implemented to monitor production and identify any deviations from standards.
3. **Final Product Testing**: Before products are shipped, final testing is conducted to verify that they meet all specified standards and performance criteria.
VI. Compliance and Certification
A. Importance of Compliance with Standards
Compliance with product standards is vital for manufacturers to ensure the safety, reliability, and performance of their fixed resistors. It also helps build trust with customers and regulatory bodies.
B. Certification Bodies and Their Roles
Several certification bodies play a crucial role in verifying compliance with product standards:
1. **Underwriters Laboratories (UL)**: UL provides safety certification for electronic components, ensuring they meet rigorous safety standards.
2. **TÜV Rheinland**: This organization offers testing and certification services for a wide range of products, including fixed resistors, focusing on quality and safety.
3. **Intertek**: Intertek provides testing, inspection, and certification services, helping manufacturers demonstrate compliance with international standards.
C. The Certification Process for Fixed Resistors
The certification process typically involves submitting samples for testing, undergoing inspections, and providing documentation to demonstrate compliance with relevant standards. Once certified, manufacturers can display certification marks on their products, signaling compliance to customers and regulatory bodies.
VII. Challenges in Meeting Product Standards
A. Variability in Manufacturing Processes
Manufacturers may face challenges in maintaining consistent quality due to variability in raw materials, production techniques, and equipment. This variability can impact the ability to meet established standards.
B. Evolving Technology and Standards
As technology advances, product standards must evolve to address new materials, manufacturing processes, and applications. Keeping up with these changes can be challenging for manufacturers.
C. Global Market Considerations
Navigating the complexities of global markets and varying regulatory requirements can pose challenges for manufacturers seeking to comply with product standards across different regions.
VIII. Future Trends in Fixed Resistor Standards
A. Innovations in Materials and Technology
The development of new materials and manufacturing techniques is likely to influence fixed resistor standards. Innovations such as nanotechnology and advanced ceramics may lead to improved performance and reliability.
B. The Impact of Sustainability and Environmental Regulations
As environmental concerns grow, standards will increasingly focus on sustainability. Manufacturers will need to adapt to regulations that promote eco-friendly practices and materials.
C. The Role of Digitalization in Standardization
Digitalization is transforming the manufacturing landscape, enabling more efficient production processes and enhanced quality control. This trend may lead to the development of new standards that leverage digital technologies for improved compliance and performance.
IX. Conclusion
In conclusion, product standards for fixed resistors are essential for ensuring the reliability, safety, and performance of these critical components in electronic circuits. Adherence to established standards not only facilitates compatibility and regulatory compliance but also enhances overall product quality. As technology continues to evolve, manufacturers must remain vigilant in adapting to new standards and challenges. The future of fixed resistor standards will likely be shaped by innovations in materials, sustainability considerations, and the ongoing digital transformation of the manufacturing industry. By prioritizing compliance with these standards, manufacturers can ensure that their products meet the demands of an ever-changing market while providing consumers with reliable and efficient electronic solutions.