What is the Mainstream Neutral Point Resistor Production Process?
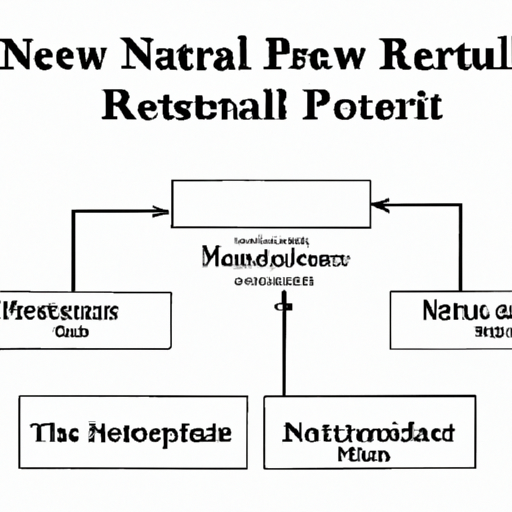
I. Introduction
Neutral Point Resistors (NPRs) are critical components in electrical systems, particularly in applications involving grounding and protection. They play a vital role in ensuring the stability and safety of power systems, especially in renewable energy setups and power electronics. Understanding the production process of NPRs is essential, as it directly impacts their reliability and performance in various applications. This blog post will delve into the mainstream production process of NPRs, exploring each stage from design to quality control, and discussing the challenges and future trends in this field.
II. Understanding Neutral Point Resistors
A. Function and Application of NPRs in Electrical Systems
NPRs serve a crucial function in electrical systems by providing a controlled path for fault currents to ground. This grounding mechanism helps protect equipment and personnel from electrical faults, ensuring the safe operation of power systems. In power electronics, NPRs are used to manage voltage levels and enhance system stability, while in renewable energy systems, they help mitigate the effects of unbalanced loads and improve overall efficiency.
B. Types of Neutral Point Resistors
NPRs can be categorized into fixed and variable types. Fixed NPRs have a predetermined resistance value, making them suitable for specific applications where consistent performance is required. In contrast, variable NPRs allow for adjustable resistance, providing flexibility in various operational conditions. The materials used in NPR production also vary, with different implications for performance, durability, and cost.
III. Overview of the Production Process
The production of NPRs involves several key stages, each contributing to the final product's reliability and performance. These stages include design and engineering, material selection, manufacturing processes, and quality control and testing. Understanding the significance of each stage is crucial for ensuring that the final product meets industry standards and customer expectations.
IV. Design and Engineering
A. Initial Design Considerations
The design phase of NPR production begins with defining electrical specifications, such as resistance values, voltage ratings, and thermal management requirements. Engineers must consider the operational environment and the specific application of the NPR to ensure optimal performance.
B. Simulation and Modeling Techniques
Advanced simulation and modeling techniques, such as Finite Element Analysis (FEA) and Computational Fluid Dynamics (CFD), are employed during the design phase. FEA helps predict how the NPR will behave under various electrical and thermal conditions, while CFD analyzes airflow and heat dissipation, ensuring that the design can effectively manage thermal loads.
V. Material Selection
A. Common Materials Used in NPR Production
The choice of materials is critical in NPR production. Common materials for resistor elements include wire-wound and film resistors, each offering distinct advantages in terms of performance and cost. Insulating materials are also essential to prevent electrical leakage and ensure safety.
B. Factors Influencing Material Choice
Several factors influence material selection, including electrical properties, thermal conductivity, and environmental resistance. For instance, materials with high thermal conductivity are preferred for applications requiring efficient heat dissipation, while those with excellent environmental resistance are essential for outdoor or harsh conditions.
VI. Manufacturing Processes
A. Overview of Manufacturing Techniques
The manufacturing process for NPRs typically involves two main techniques: wire-wound resistor fabrication and film resistor production. Wire-wound resistors are made by winding a resistive wire around a core, while film resistors are created by depositing a thin film of resistive material onto a substrate.
B. Assembly Processes
Once the resistor elements are produced, they undergo assembly processes, which include component integration and soldering. Proper connections are crucial for ensuring electrical integrity and performance.
C. Automation in NPR Production
Automation plays a significant role in NPR production, with robotics and machinery enhancing efficiency and precision. Automated processes reduce human error and increase production speed, allowing manufacturers to meet growing demand while maintaining high-quality standards.
VII. Quality Control and Testing
A. Importance of Quality Assurance in NPR Production
Quality assurance is paramount in NPR production, as any defects can lead to failures in electrical systems. Manufacturers implement rigorous quality control measures to ensure that each NPR meets the required specifications.
B. Testing Methods for NPRs
Testing methods for NPRs include electrical testing, which assesses resistance and voltage ratings, and thermal testing, which evaluates heat dissipation and thermal cycling. These tests help identify potential issues before the NPRs are deployed in the field.
C. Certification and Compliance with Industry Standards
Compliance with industry standards is essential for NPR manufacturers. Certifications from recognized organizations ensure that the products meet safety and performance requirements, providing customers with confidence in their reliability.
VIII. Challenges in NPR Production
A. Common Challenges Faced During Production
NPR production is not without its challenges. Common issues include material sourcing and cost fluctuations, which can impact production timelines and budgets. Additionally, technological advancements require manufacturers to adapt their processes continually.
B. Strategies to Overcome These Challenges
To address these challenges, manufacturers invest in research and development to explore new materials and production techniques. Collaborating with suppliers and industry partners also helps mitigate risks associated with material sourcing and cost management.
IX. Future Trends in NPR Production
A. Innovations in Materials and Manufacturing Techniques
The future of NPR production is likely to see innovations in materials and manufacturing techniques. Researchers are exploring advanced materials that offer improved performance and durability, while new manufacturing methods may enhance efficiency and reduce costs.
B. The Impact of Sustainability on NPR Production
Sustainability is becoming increasingly important in NPR production. Manufacturers are seeking eco-friendly materials and processes to minimize their environmental impact, aligning with global trends toward sustainability in the electrical industry.
C. Predictions for the Future of NPR Technology
As technology continues to evolve, the demand for more efficient and reliable NPRs will grow. Future developments may include smarter NPRs equipped with sensors for real-time monitoring, enhancing their functionality in modern electrical systems.
X. Conclusion
In summary, the production process of Neutral Point Resistors is a complex and multifaceted endeavor that encompasses design, material selection, manufacturing, and quality control. NPRs play a significant role in modern electrical systems, ensuring safety and stability in various applications. As the industry evolves, manufacturers must adapt to new challenges and embrace innovations to meet the demands of the future. The ongoing evolution of NPR technology promises to enhance the reliability and efficiency of electrical systems, paving the way for a more sustainable and advanced energy landscape.
XI. References
A comprehensive list of relevant literature, industry standards, and expert opinions can be found in the references section. For those seeking a deeper understanding of NPR production, suggested further reading includes technical papers, industry reports, and textbooks on electrical engineering and materials science.
What is the Mainstream Neutral Point Resistor Production Process?
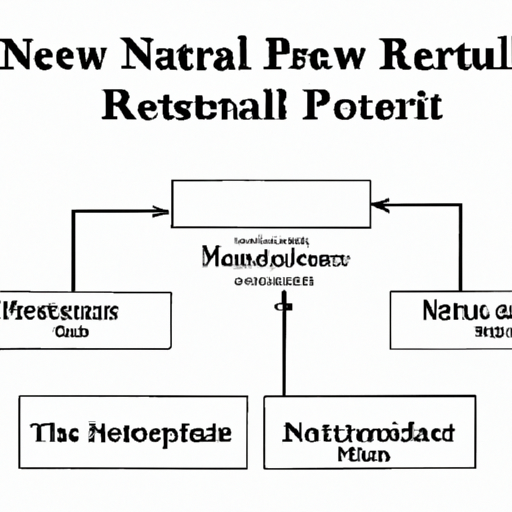
I. Introduction
Neutral Point Resistors (NPRs) are critical components in electrical systems, particularly in applications involving grounding and protection. They play a vital role in ensuring the stability and safety of power systems, especially in renewable energy setups and power electronics. Understanding the production process of NPRs is essential, as it directly impacts their reliability and performance in various applications. This blog post will delve into the mainstream production process of NPRs, exploring each stage from design to quality control, and discussing the challenges and future trends in this field.
II. Understanding Neutral Point Resistors
A. Function and Application of NPRs in Electrical Systems
NPRs serve a crucial function in electrical systems by providing a controlled path for fault currents to ground. This grounding mechanism helps protect equipment and personnel from electrical faults, ensuring the safe operation of power systems. In power electronics, NPRs are used to manage voltage levels and enhance system stability, while in renewable energy systems, they help mitigate the effects of unbalanced loads and improve overall efficiency.
B. Types of Neutral Point Resistors
NPRs can be categorized into fixed and variable types. Fixed NPRs have a predetermined resistance value, making them suitable for specific applications where consistent performance is required. In contrast, variable NPRs allow for adjustable resistance, providing flexibility in various operational conditions. The materials used in NPR production also vary, with different implications for performance, durability, and cost.
III. Overview of the Production Process
The production of NPRs involves several key stages, each contributing to the final product's reliability and performance. These stages include design and engineering, material selection, manufacturing processes, and quality control and testing. Understanding the significance of each stage is crucial for ensuring that the final product meets industry standards and customer expectations.
IV. Design and Engineering
A. Initial Design Considerations
The design phase of NPR production begins with defining electrical specifications, such as resistance values, voltage ratings, and thermal management requirements. Engineers must consider the operational environment and the specific application of the NPR to ensure optimal performance.
B. Simulation and Modeling Techniques
Advanced simulation and modeling techniques, such as Finite Element Analysis (FEA) and Computational Fluid Dynamics (CFD), are employed during the design phase. FEA helps predict how the NPR will behave under various electrical and thermal conditions, while CFD analyzes airflow and heat dissipation, ensuring that the design can effectively manage thermal loads.
V. Material Selection
A. Common Materials Used in NPR Production
The choice of materials is critical in NPR production. Common materials for resistor elements include wire-wound and film resistors, each offering distinct advantages in terms of performance and cost. Insulating materials are also essential to prevent electrical leakage and ensure safety.
B. Factors Influencing Material Choice
Several factors influence material selection, including electrical properties, thermal conductivity, and environmental resistance. For instance, materials with high thermal conductivity are preferred for applications requiring efficient heat dissipation, while those with excellent environmental resistance are essential for outdoor or harsh conditions.
VI. Manufacturing Processes
A. Overview of Manufacturing Techniques
The manufacturing process for NPRs typically involves two main techniques: wire-wound resistor fabrication and film resistor production. Wire-wound resistors are made by winding a resistive wire around a core, while film resistors are created by depositing a thin film of resistive material onto a substrate.
B. Assembly Processes
Once the resistor elements are produced, they undergo assembly processes, which include component integration and soldering. Proper connections are crucial for ensuring electrical integrity and performance.
C. Automation in NPR Production
Automation plays a significant role in NPR production, with robotics and machinery enhancing efficiency and precision. Automated processes reduce human error and increase production speed, allowing manufacturers to meet growing demand while maintaining high-quality standards.
VII. Quality Control and Testing
A. Importance of Quality Assurance in NPR Production
Quality assurance is paramount in NPR production, as any defects can lead to failures in electrical systems. Manufacturers implement rigorous quality control measures to ensure that each NPR meets the required specifications.
B. Testing Methods for NPRs
Testing methods for NPRs include electrical testing, which assesses resistance and voltage ratings, and thermal testing, which evaluates heat dissipation and thermal cycling. These tests help identify potential issues before the NPRs are deployed in the field.
C. Certification and Compliance with Industry Standards
Compliance with industry standards is essential for NPR manufacturers. Certifications from recognized organizations ensure that the products meet safety and performance requirements, providing customers with confidence in their reliability.
VIII. Challenges in NPR Production
A. Common Challenges Faced During Production
NPR production is not without its challenges. Common issues include material sourcing and cost fluctuations, which can impact production timelines and budgets. Additionally, technological advancements require manufacturers to adapt their processes continually.
B. Strategies to Overcome These Challenges
To address these challenges, manufacturers invest in research and development to explore new materials and production techniques. Collaborating with suppliers and industry partners also helps mitigate risks associated with material sourcing and cost management.
IX. Future Trends in NPR Production
A. Innovations in Materials and Manufacturing Techniques
The future of NPR production is likely to see innovations in materials and manufacturing techniques. Researchers are exploring advanced materials that offer improved performance and durability, while new manufacturing methods may enhance efficiency and reduce costs.
B. The Impact of Sustainability on NPR Production
Sustainability is becoming increasingly important in NPR production. Manufacturers are seeking eco-friendly materials and processes to minimize their environmental impact, aligning with global trends toward sustainability in the electrical industry.
C. Predictions for the Future of NPR Technology
As technology continues to evolve, the demand for more efficient and reliable NPRs will grow. Future developments may include smarter NPRs equipped with sensors for real-time monitoring, enhancing their functionality in modern electrical systems.
X. Conclusion
In summary, the production process of Neutral Point Resistors is a complex and multifaceted endeavor that encompasses design, material selection, manufacturing, and quality control. NPRs play a significant role in modern electrical systems, ensuring safety and stability in various applications. As the industry evolves, manufacturers must adapt to new challenges and embrace innovations to meet the demands of the future. The ongoing evolution of NPR technology promises to enhance the reliability and efficiency of electrical systems, paving the way for a more sustainable and advanced energy landscape.
XI. References
A comprehensive list of relevant literature, industry standards, and expert opinions can be found in the references section. For those seeking a deeper understanding of NPR production, suggested further reading includes technical papers, industry reports, and textbooks on electrical engineering and materials science.